Additive manufacturing of plastics in SMEs
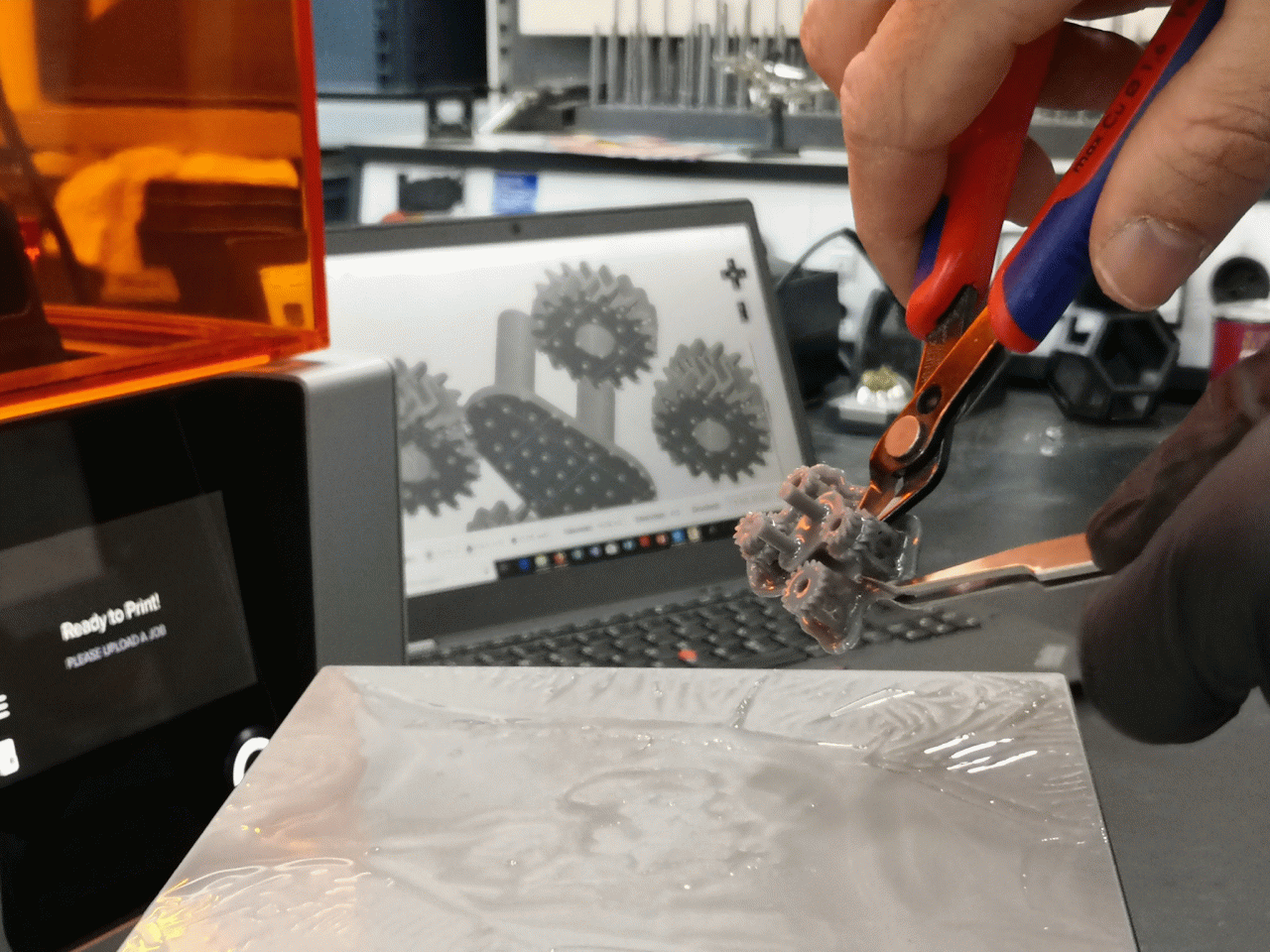
The advantages of additive manufacturing are already being researched in projects at research institutes and discussed in publications. However, small and medium-sized enterprises (SMEs) in particular lack the necessary information to invest sustainably in this future technology.
Experimental laboratory
The experimental laboratory sponsored by the Hannover Region aims to demonstrate the possibilities and limitations of additive manufacturing to companies in a practice-oriented manner in order to raise their awareness of the use of this technology. At regular networking events, specialists and managers from all regional companies can find out about the results of the demonstrator projects and discuss new project ideas with other participants.
Additive manufacturing or 3D printing describes a group of processes in which components are built up layer by layer from metallic or plastic-based materials. Powder, synthetic resin or plastic strands, known as filaments, are usually used as the starting material.
Localized melting or hardening takes place using heated nozzles or lasers. Subsequent cooling solidifies the material in the originally intended form. Technologically, all conceivable components can be produced using these processes.
So far, additive manufacturing has only proven to be economically viable when individualized components or small quantities are required. However, the use of 3D printers is becoming more and more established in larger companies, which is why the specific possibilities of additive manufacturing are increasingly becoming the focus of design engineers. More and more components are being developed that can only be produced additively.
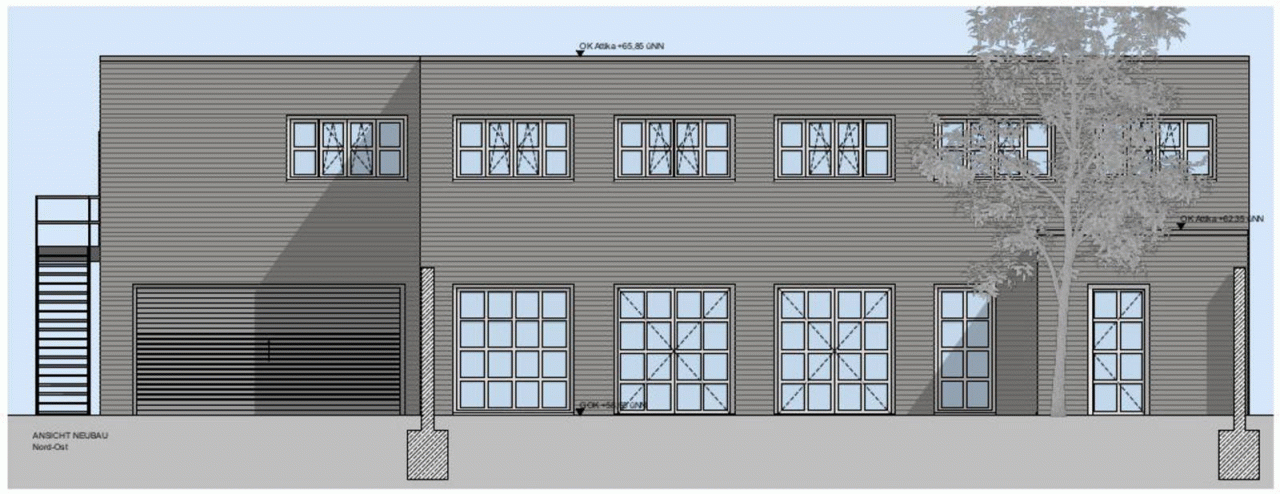
A core element of the "Additive manufacturing of plastics in SMEs" project is the permanent establishment of an experimental laboratory, which employees of local production companies can use to gain their own experience with additive manufacturing.
The experimental laboratory will be realized in 2020 in Hanover-Linden and consists of training rooms and a workshop. The use of software, 3D printers and suitable materials will be taught in workshops. Components that interested parties bring with them by prior arrangement can also serve as sample applications. These are redesigned to suit additive manufacturing and produced on suitable equipment in the workshop. The consortium uses various systems from different manufacturers for this purpose.
The planned projects represent a cross-section of the entire field of application of additive manufacturing. The issues planned so far include the feasibility of additively manufactured electronic components, the optimization of products made from bioplastics for end customers, the additive manufacturing of difficult-to-machine plastics and the production of assembly aids.
In all application examples, the focus is not just on the printing process itself. Instead, the entire process chain, from component design to post-processing, is always taken into account. In addition, the focus is not only on technical feasibility but also on economic benefits. So far, 6 companies have already expressed their interest in participating in the project with an application. Interested companies can submit ideas for additional projects at any time via the contact person.
Up to three dates are planned each year, which will take place in the experimental laboratory or in the companies in which the demonstrator projects have been implemented.
Each of the two- to three-hour events will focus on a different topic. Dates have already been planned with focal points such as "Potentials of additive manufacturing", "Energy efficiency through 3D printing", "Use of bio-based plastics" and "Additive manufacturing in prototype construction" or "3D printing in electronics production". Further dates and topics are being planned. The current network is open.
In addition to existing interested parties, companies and institutes that have not yet participated can therefore also get involved as hosts.
Additive manufacturing processes offer numerous positive approaches for resource-saving production and a reduction in CO2 emissions. The additive design of components enables lightweight construction, which saves material. Its often CO2-intensive production is no longer necessary.
The replacement of metallic materials with high-performance plastics or fiber-reinforced plastics leads to an additional reduction in weight. As additively processed plastics can be melted down and reused, material cycles can be closed within a region.
The extensive use of additive manufacturing systems in companies enables economical and decentralized component production. This saves CO2 emissions that would otherwise be caused by transportation by truck.
By implementing the project, the Hannover Region is pursuing the goal of creating a network of manufacturing companies that can make a realistic assessment of additive manufacturing. All information events are therefore available free of charge.
Contact
Dr. Michael Merwart
Hanover Region
Economic Development
Department of Economic Development and Employment Promotion
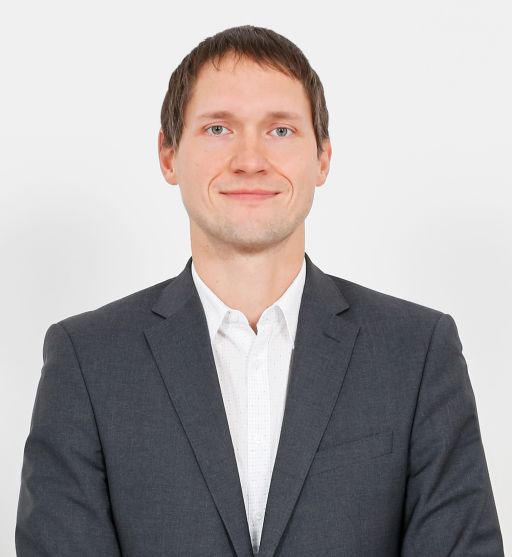