Environmentally conscious autonomy: Hannover Region supports 3D printing at MediTECH
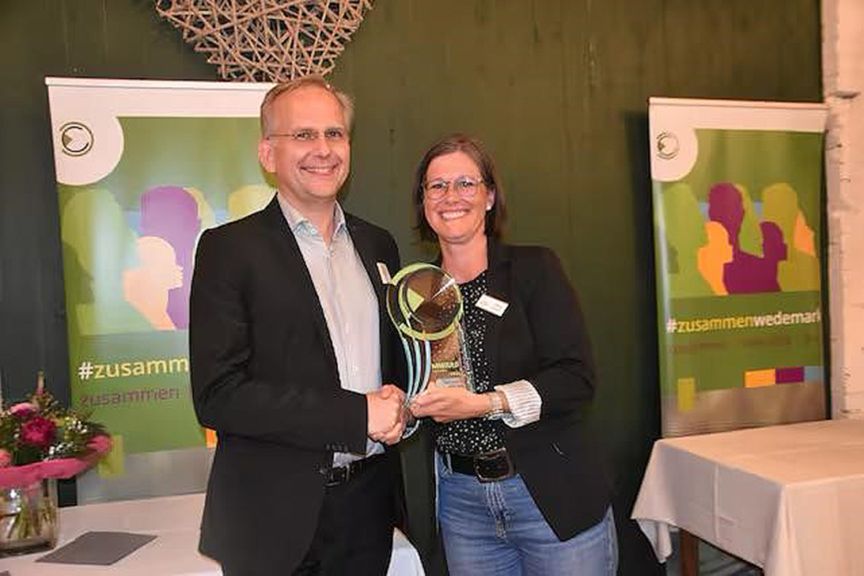
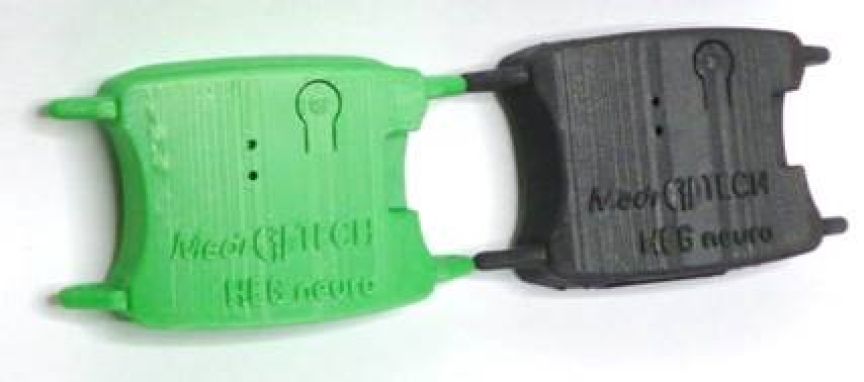
MediTECH Electronic GmbH is an SME from the Hanover region. The company was founded in 1996 by Ralph and Karen Warnke and is an owner-managed family business active in the field of special medical technology solutions and hearing and perception support. MediTECH is very active in research and innovation and is constantly carrying out new research and development projects with national and international partners. Rapid knowledge and implementation processes are also important here. The aspect of creating individual production parts in particular is becoming increasingly important. In recent R&D projects, it has become clear that delays and, in particular, recurring iteration loops with multiple shipping routes between external 3D printing services could be greatly helped by an in-house 3D printing solution tailored to the company, its specific requirements and issues.
A detailed market and technology analysis was carried out as part of the HRGE funding from the Hannover Region Economic Development Agency. This was compared with the company's internal requirements in the context of 3D printing. Particular attention was paid to resource-saving and environmentally friendly solutions.
MediTECH's goal is to research and gain expertise in the field of 3D printing and to implement a specific technology with the aim of being able to produce prototypes and small series with individual housing solutions in a resource-saving manner. Recently, MediTECH has increasingly started to create individual housing solutions for the hardware developed in-house. The first solution implemented to date for a NIRS-based sensor for neurofeedback was created in a custom housing with a push button flexibly inserted into the housing, a suitable LED opening and ergonomics optimized for the application in several iteration stages with external support. The product branding was crowned by a raised display of the product name and the company logo.
The ability to create such individual housings for significantly larger products using 3D printing, in addition to conventional injection molding solutions, will strengthen the company's development expertise and competitiveness in the long term. In the future, prototypes can be realized in a resource-saving manner and, ideally, series production can be ensured in-house.
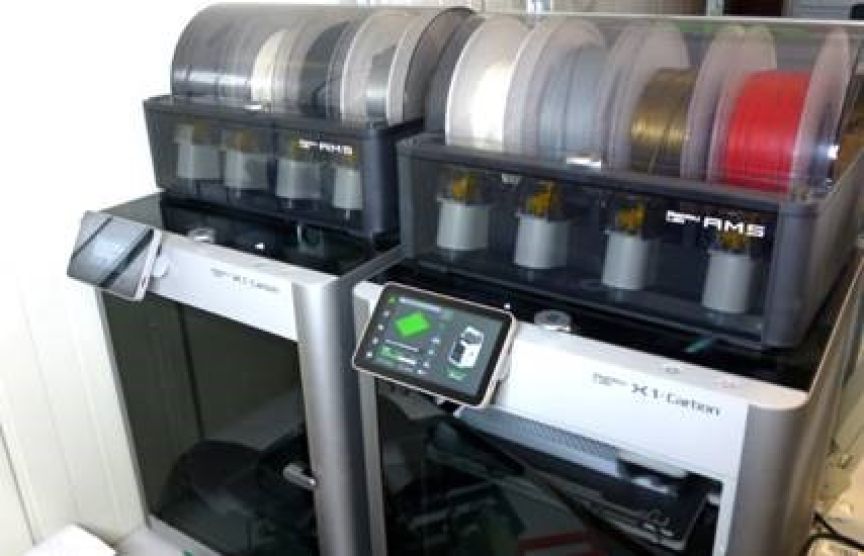
A particular challenge in the project was the selection of the right and future-oriented technology platform. In addition, the project had to work out whether and which machining and finishing processes needed to be solved in-house or, if necessary, provided by external services after housing production. The corporate objective is to work out and implement the most economical, ecological and autonomy-promoting process for the company.
The operational integration of an in-house 3D printing structure promotes the company's autonomy, especially in light of the current supply chain situation. The R&D process becomes significantly more independent and flexible with regard to design aspects. Expenses for shipping and external services are significantly reduced. Highly customized products can be created competitively and economically in-house, which creates and secures additional work potential. In addition, the 3D printer can save valuable resources compared to the previous injection molding process.
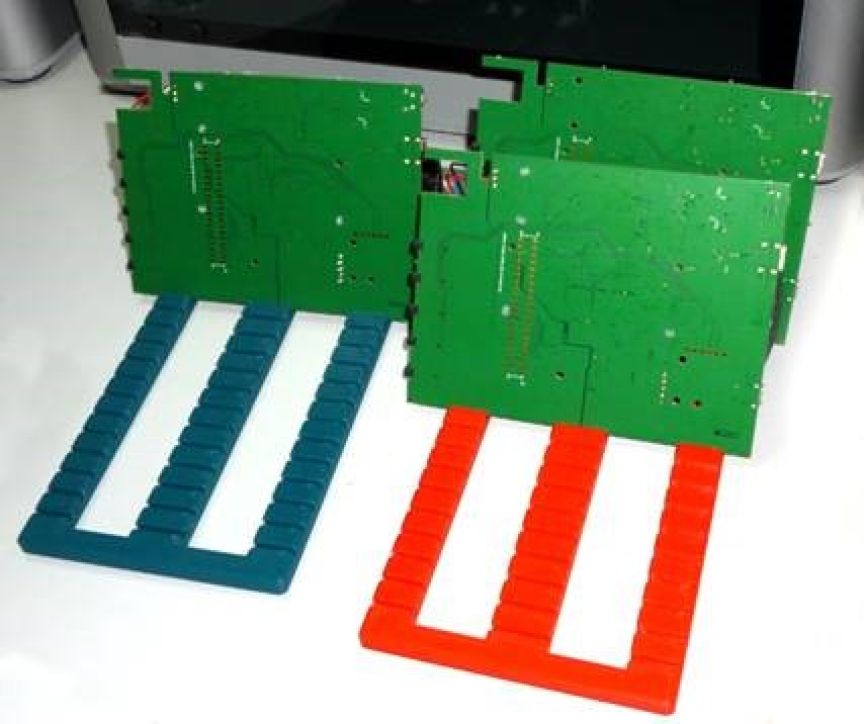
At the end of an intensive analysis and evaluation process with various surprising experiences regarding the technologies available on the market, the underlying price-performance ratio and the possibilities and limitations for MediTECH, a system was ultimately found and purchased that has been providing the company with support far beyond the original approach to housing production since the 4th quarter of 2023. In addition to the aspect of prototype housing production, trays for PCBs for final assembly and final testing processes, for example, are now created and stored in a customized manner. Small, individual and spare parts, some of which are otherwise difficult or impossible to procure (especially in small quantities and due to existing supply chain problems), can now be produced and perfected in-house on a daily basis.
The chosen solution offers the use of very different materials and degrees of hardness, can integrate various colors and make components that would otherwise be difficult to define and procure available to the company live in many places. The expertise in dealing with corresponding print/step files is an additional knowledge gain for the company.
It is a very valuable experience to make this technology accessible to students in specific project tasks and also to use it specifically in the course of Bachelor's and Master's theses - for example as part of engineering courses or work in the field of biomedical engineering.
Overall, the project was a complete success for MediTECH - thanks to the support of the Hannover Region, the company now has more know-how, a better infrastructure and a sustainable and value-adding solution in the field of 3D printing, which in turn also enables students to gain additional practical experience and knowledge beyond the company.
Contact us
Dr. Jöran Wrana
Hanover Region
Economic Development
Department of Economic Development and Employment Promotion
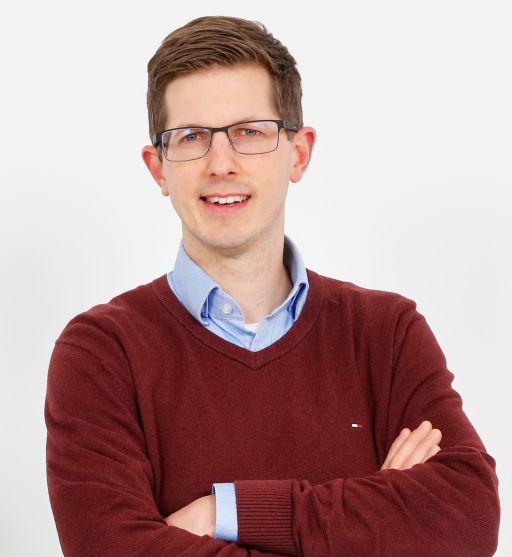